Why Choose Nescon Road Cleaning Trucks?
You may be wondering, why choose Nescon’s XBroom over other street sweepers? The XBroom offers several advantages over the competition. This includes the longest sweep time, largest hopper and extremely rugged construction.
What sets us apart?
Hydraulic System
With three pumps, each one only operates at the minimum pressure needed to carry the load. One pump runs the gutter brooms, one runs the elevator, and one runs the main broom.
Elevator Wear. Results up to 10.8 million revolutions on elevator before rebuild while sweeping millings/road grindings.
Hopper Capacity
Largest hopper capacity in its class. Total volume of 5.9 Cubic Yards with usable net capacity of 4.9 CY.
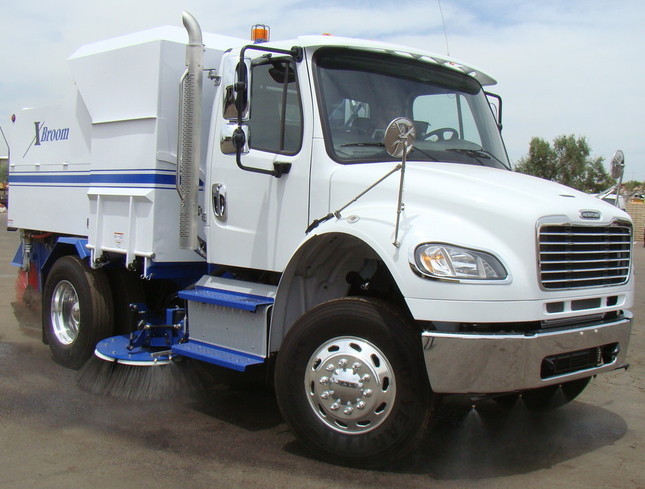
Standard Features
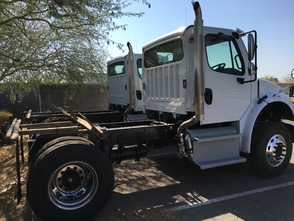
Truck Chassis
The X-Broom is built on a dependable Freightliner M2 chassis. The Freightliner chassis includes a 300 HP, 860 Ft-lb torque Cummins 8.9L engine that meets current emissions standards. The Cummins engine uses SCR technology that utilizes DEF fluid. This M2 Chassis also carries a 50 gallon fuel tank, Allison 3500 Series transmission, power and heated mirrors, dual steering and controls, Air Ride Rear Suspension, and 23,000 lb 2-speed rear axle.
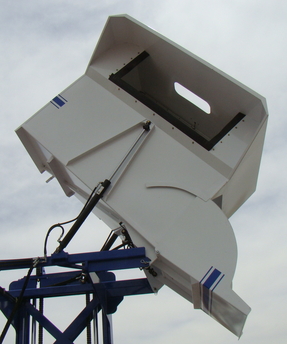
Hopper
Largest hopper capacity in its class. Total volume of 5.9 Cubic Yards with USABLE net capacity of 4.9 CY. Our unique lift design allows for increased hopper volume which means more time sweeping and less time dumping. A full width discharge door measuring (42″W x 42″L) to dump load in the center of truck. Dual hydraulic door cylinders. Hopper loading can be viewed from the cab window or two access doors on either side. The hopper can be dumped from any height. The hopper floor is a formed 3/16” plate for extra strength.
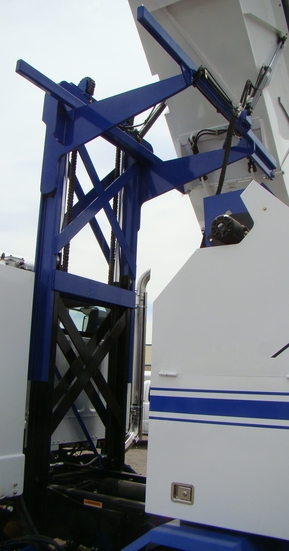
Lift System
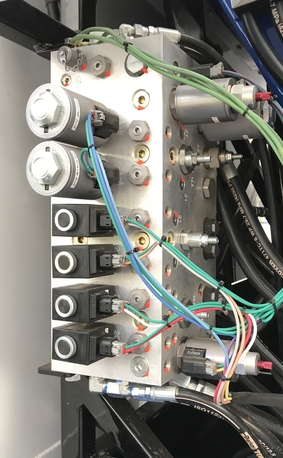
Hydraulic System
The broom uses three separate hydraulic pumps. Pump 1 runs the gutter brooms (450psi), Pump 2 runs the elevator (450psi), and Pump 3 runs the main broom (250psi). Each pump is a pressure compensated, variable Displacement piston style Rexroth pump. This is much more efficient than using only one pump like most other sweepers. With three pumps, each one only operates at the minimum pressure needed to carry the load. The lower horsepower required with our design saves fuel and allows the engine to operate at factory idle and eliminates brake riding to manually increase hydraulic output. There are two very accessible hydraulic manifolds mounted opposite each other on the Sub-Frame of the XBroom. This puts the valves very close to the motors or cylinders minimizing the lengths of hoses, reducing the likelihood of pinching or chafing. The 45 gallon hydraulic tank is mounted directly behind the cab, high on the left side. This keeps the tank away from the dirt and provides better suction flow to the pumps and also acts in part to dissipate heat through the surface area of the tank. There is a large in-tank 10-micron return filter, glass sight level with a thermometer, and an in-tank float and over-temperature switch for operator warning indicators. A digital Hydraulic temperature gauge is also displayed on the Main Operation Screen of the PLC. Proportional Integrated Speed Controls are a standard option found on the XBroom. This Allows for In-Cab control of hydraulic speeds from the touch screen PLC.
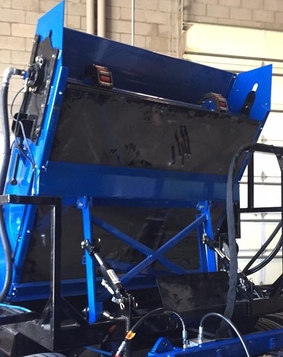
Elevator System
The elevator is a full 60″ drag slat type conveyor. Unique features include 14 replaceable rubber squeegee flights, poly-urethane shaft sprockets, and dual roller chain. The elevator is driven hydraulically with a rigid coupling and torque rod. No chains or sprocket for the motor drive to wear out and replace. The elevator jam indicator is standard and doubles as a speed pickup that is digitally displayed through the Main Operations Screen of the PLC. The speed of the conveyor is variable and can be reversed from a toggle switch located on the PLC or on the touch screen display. The elevator sweeping height is able to be raised and lowered from the cab. The sweeping height can be set into the PLC and this height will be repeated each time the elevator is lowered to sweep.
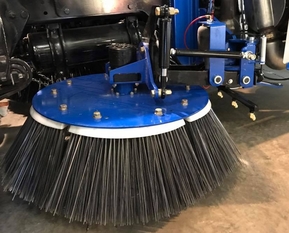
Gutter Brooms
The gutter brooms are a full floating, trailing arm, air suspended design. The gutter broom speed is variable and the down pressure can be adjusted from the cab. The extension of the gutter brooms are air powered and the width is infinitely adjustable via a manual stop adjuster. The steel broom disk protects from curb strikes and has mounting holes for either 4 or 5 segment replaceable gutter brooms. Each gutter broom has hydraulic tilt function left or right from the cab. No failure prone electric actuators.
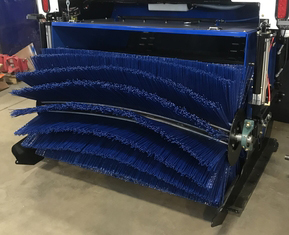
Main Broom
The main broom is a full 60” wide with replaceable poly or steel wafers (Stock). Several other main broom options are available upon request including (Strip Mandrel Core, Tube Mandrel Core, Cable Wrap Core) The lift and suspension of the broom is achieved with pneumatic cylinders. The sweeping down pressure is adjusted by individual left and right side precision regulators and pressures from these are relayed back to the PLC and can be monitored & Adjusted from the operators station. Broom adjustments are much easier with this system than the springs, chains, and adjustment bolts of other systems. The main broom air suspension will automatically compensate as the broom wears in Auto Mode or can be changed to Manual run mode. The broom is driven using a floating hydraulic motor that is rigid coupled to the broom shaft. This eliminates the wear and replacement of chains and sprockets.
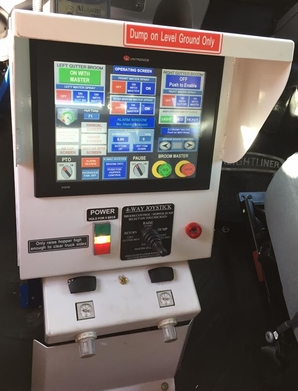
Control System
One of the most integral parts of our advanced street sweeping technology is the industrial grade Programmable Logic Controller or (PLC), with it’s touch-screen display panel. All functions of the broom are controlled by the PLC. This enables fully automatic operation of the sweeping system. Push down once on the Joystick and the PLC activates the functions needed to sweep. This involves starting, lowering, and extending the gutter brooms, starting the elevator and lowering to the desired height, lowering the skid shoes and main broom, starting the broom motor, opening the water spray valves and starting the water pump(s). The PLC always monitors the position of the elevator, ensuring that it is fully engaged with the Hopper before starting. It also monitors the hydraulic temperature and level and will raise all brooms if the transmission is placed in Reverse. There is a “Pause” button that will stop the brooms and water sprays if the sweeper has to stop for traffic without raising the brooms or elevator. The “Stop” button will stop and raise all brooms and the elevator will continue to run for 6 seconds to empty out.
The PLC has a resettable hour meter for each broom, the elevator, water pump, hydraulic fan, and PTO. The PLC also keeps a count on how many times the hopper has dumped. This lets you track broom wear to actual operating hours of the individual broom allowing for cost analysis.
There is a screen for Manual Operation of each function for testing and diagnostics. The buttons also gives a visual indication of what is “on” and the status of each limit switch. The PLC greatly simplifies the wiring to the valves and solenoids on the broom.
The hopper dumping functions can be either be controlled from the touch-screen or from a joystick on the front panel. When the hopper needs to be dumped, the PLC will move the elevator back before raising the hopper, then ensure the hopper is down before moving the elevator to the forward position.
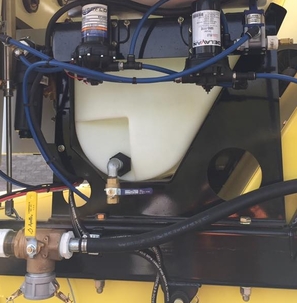
Water System - PM10 Certified
The water system consists of two electric pumps, this allows the operator to select an “Economy” mode for standard sweeping conditions or a “Max” mode for dusty sweeping conditions. The standard water tank is 300 gallons. The pumps can run dry without damage. A front 5 tip Hollow Cone spray bar is standard as well as 3 tip Hollow Cone spray bars on each gutter broom and a 5 tip V-Jet spray bar is used on the main broom. The system pumps and tips are designed for misting and encapsulating dust particles utilizing a smaller drop size. This allows our water system to do a great job at suppressing dust while minimizing water use and not creating muddy conditions.
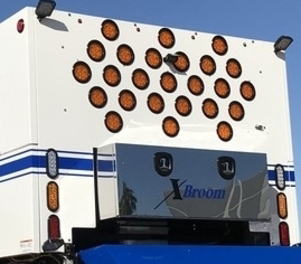
Arrow Board
There are two types of arrow boards available on the X-Broom. The standard arrow board consist of 13 oval amber lights. There is also an optional 25 round light arrow board with advanced flash capabilities (Seen in picture to the Left). The Standard/Advanced Button found in the SETUP screen allows for pattern changes on only the Advanced arrow board option. Patter Options Include (Chevrons, Sequencing Arrows Left and Right, Sequencing Bar, Diamonds) Arrow board functions can be interlocked with the PTO operation so the Arrow board is automatically disabled while in driving mode.